Working principle of hydraulic overload protection device
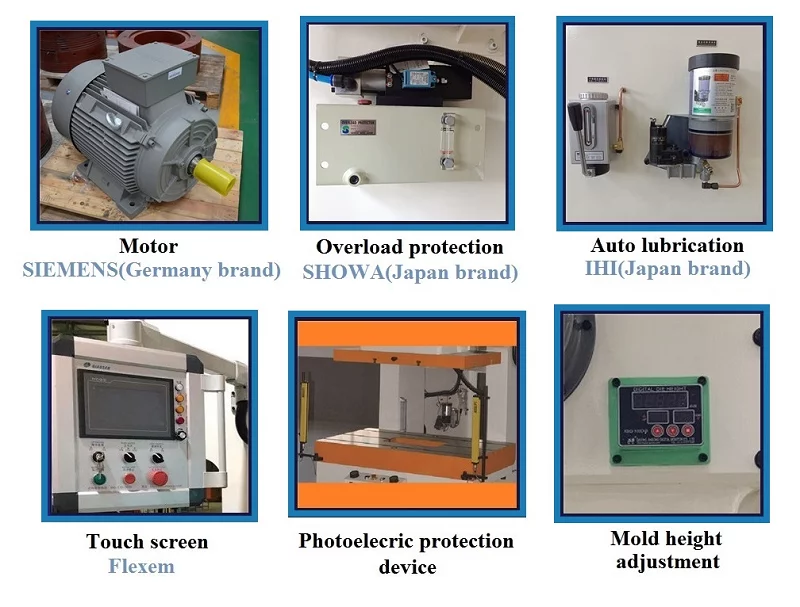
Old-fashioned overload protection devices in mechanical presses, such as the crushing block type, are gradually being eliminated because they cannot accurately send signals and effectively protect the machine tool, and replacement is very troublesome. It is replaced by a hydraulic overload protection system that can unload quickly and recover quickly.
1. System composition and working principle
The hydraulic overload protection system generally consists of pneumatic pumps, unloading valves, pressure relays, solenoid valves, pressure gauges and other components.
1. Air source 2. Lubricator 3. Solenoid valve 5. Pressure reducing valve 6. Pneumatic pump 7. Muffler 8. Oil tank 9. Oil filter 10. Stop valve 11. Inlet and outlet oil check valve 13. Check check Directional valve 15. Unloading valve 16. Pressure relay 17. Pressure gauge and buffer valve 18. Hydraulic cylinder
When the mold height is improperly adjusted or double materials occur, the press will be overloaded. At this time, the pressure in the hydraulic cylinder rises sharply, and the pressure in the high-pressure chamber of the unloading valve is greater than the back pressure in the back-pressure chamber, pushing the piston downward to open the oil return port, and the hydraulic oil quickly drains back to the tank. Under the action of the balancer, the slider moves up 20mm to protect the press and mold from damage; at the same time, the pressure relay and travel switch act to cut off the clutch control circuit and the press stops; the solenoid valve closes the air source and quickly discharges the unloading There is air in the valve back pressure chamber, the "normal" indicator light is off, the "unloading" indicator light is on, and the press cannot be started.
After the press fault is eliminated, turn the hydraulic protection switch of the control station to the "reset" position, start the "inching" stroke, and raise the slider to the top dead center. At this time, the solenoid valve is connected to the air source, and the compressed air enters the lower chamber of the unloading valve, causing the piston to rise and reset, closing the oil return channel of the hydraulic cylinder; at the same time, the compressed air enters the pneumatic pump, pushing the pneumatic piston to reciprocate, thereby driving the hydraulic plunger to reciprocate. . As a result, the low-pressure oil is sucked into the tank, output to the hydraulic cylinder through the one-way valve, and gradually increased to the specified pressure. At this time, the hydraulic pad is reset, the pressure relay and the travel switch of the unloading valve operate, the hydraulic protection "unloading" indicator light goes out, the "normal" indicator light turns on, and the hydraulic overload protection system returns to normal. Turn the hydraulic protection work selection switch to the "normal" position, and the press can work normally. It only takes about 3 minutes for the hydraulic overload protection system to recover each time, which can meet the requirements of general high-efficiency stamping production.
8years foriegn trade experience Easily grasp customer needs Keeping good relationship with customers