How to Solve the Problem of Mold Sticking in Precision Punch Press
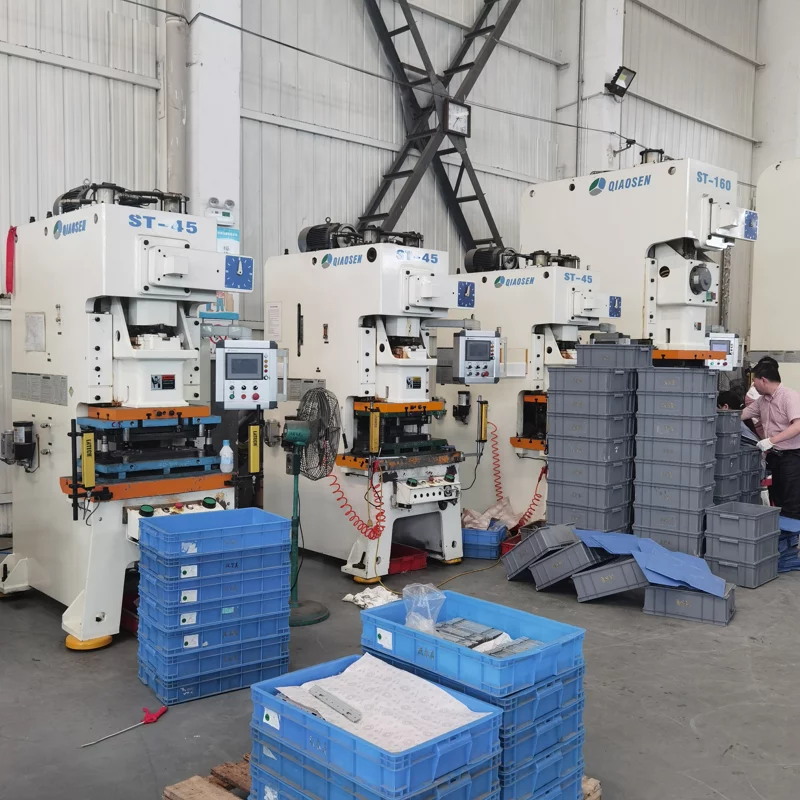
In actual use, improper use and operation of precision punch presses often result in mold sticking, which prevents the upper die from being lifted quickly and requires downtime for mold repair, greatly reducing the effective working time for stamping and causing production to fall behind schedule. Currently, many manufacturers of precision punch presses have proposed solutions, such as installing anti-blocking adjustment devices on the sub-die of precision punch presses. By installing plain bearings between the screw fixing block and the sub-die screw, the relative friction between the screw fixing block and the screw can be greatly reduced, avoiding mold blocking. However, there is no dedicated anti-blocking device specifically designed for precision punch presses. When the mold is stuck, it cannot be quickly resolved, which causes great inconvenience to the use of precision punch presses.
To address this issue, a reverse electrical control system equipped with a mold detection device has been added to the production design and manufacturing of precision punch presses. For precision punch presses equipped with reverse electrical control systems, when the mold detector detects that the mold is stuck in the precision punch press, it sends a signal to the PLC program controller, and the PLC program controller controls the main motor to reverse the on-off process. At this time, the main motor reverses, and the upper die installed on the slide of the precision punch press is lifted under the effect of the main motor's reversal, effectively solving the problem of mold sticking in the actual use of precision punch presses.
This solution not only effectively resolves the issue of mold sticking in precision punch presses but also improves production efficiency by reducing the downtime required for mold repair. The addition of the mold detection device and the reverse electrical control system provides a real-time monitoring and control mechanism for mold status in precision punch presses. When the mold is stuck, the system automatically detects it and initiates the reverse operation of the main motor, lifting the upper die and allowing the production process to continue without interruption.
In conclusion, the problem of mold sticking in precision punch presses can be effectively solved by implementing an anti-blocking adjustment device or a reverse electrical control system with a mold detection device. This not only reduces the downtime caused by mold repair but also improves production efficiency by ensuring continuous operation of precision punch presses. As a result, manufacturers can meet the demand for precision stamping and maintain a smooth production flow.
8years foriegn trade experience Easily grasp customer needs Keeping good relationship with customers