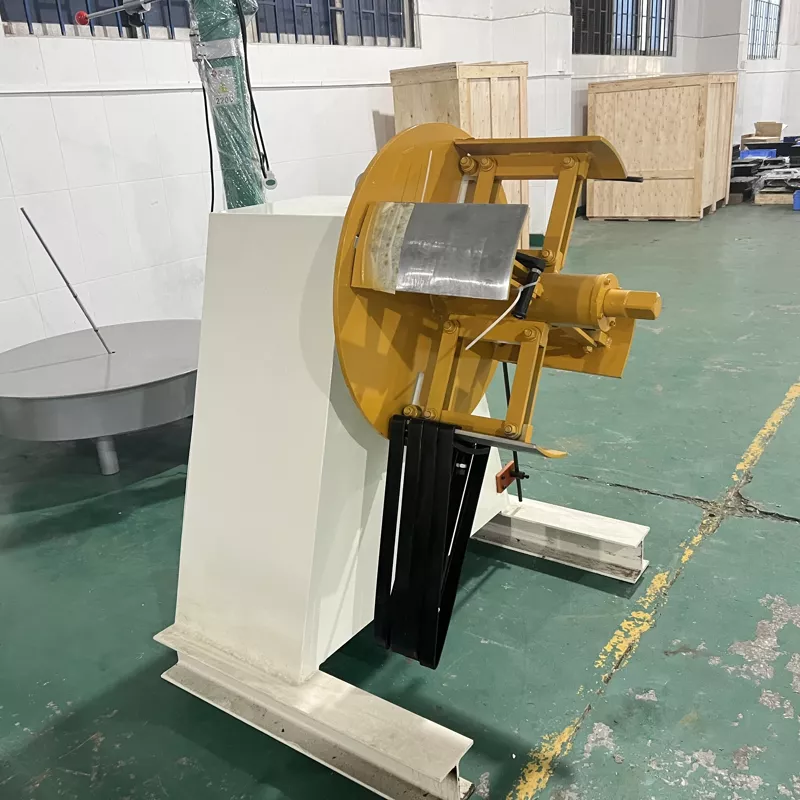
The steel decoiler machine is a marvel of modern industrial machinery, constituting six crucial elements: a sturdy base, an anchored support frame, an adaptive expansion and contraction system, an efficient drive mechanism, a cutting-edge electrical control box, and a high-precision sensor. The support frame, securely fastened to the material rack base, hosts an innovative expansion and contraction mechanism. Inside, there lies an agile drive mechanism, composed of a motor coupled with a reduction gear. An advanced electrical control box is conveniently installed on one side, while a precision sensor is affixed firmly underneath.
The beating heart of the steel decoiler machine is the versatile expansion and contraction mechanism, charged with managing, broadening, and unwinding the material. The central figure of its composition is a rotating shaft, featuring threading at one end. The shaft is surrounded by a revolving sleeve, robustly fastened to an adjusting bolt on its terminus, thus aligning with the threaded portion of the shaft. Rotating sleeve features well-arranged grooves, hosting sliders. Numerous rotating rods are pivotally connected to these sliders. Every rod’s opposing end attaches to one of four supporting plates. Guiding support wheels are strategically placed on the shaft, each featuring a guiding arc-shaped aperture. Supporting plates’ terminus boast guiding blocks that coincide with the arc-shaped apertures. Flanking blocks are tailored to match the guiding plates. The mechanism’s expansion and contraction is a matter of simple manual adjustment of the bolt; starting with counter-clockwise movement to shrink the internal diameter for material accommodation, followed by a clockwise adjustment to secure the material roll. Once the material is upheld by the tile-supporting plate, four type-A iron stoppers restrict material displacement.
Housed within the machine’s innovative electrical control box lies an array of electrical components, including an AC contactor, a transformer, a time relay, an intermediate relay, and adjustment buttons. These synchronize seamlessly with a sensor rod positioned at the machine’s lower end, facilitating automated sensory control. The time relay’s delay period governs the material feed rate, and the sensor rod’s height is modifiable to manage the feeding length efficiently.
In practical terms, the operator of the steel decoiler machine manually turns the handle to constrict and expand the drum for material lodging. The motor’s reduction gear propels the primary shaft to unwind via the transmission chain, and the material is fed in an upward direction. The feeding material engages with the sensor rod, which, upon contact and subsequent detachment of the material, triggers the start-stop control. This operation harmonizes with the follow-up leveling machines and feeding machines, paving the way for a fully automated manufacturing and processing workflow.
8years foriegn trade experience Easily grasp customer needs Keeping good relationship with customers