The Difference Between Servo Press and Conventional Pneumatic Press
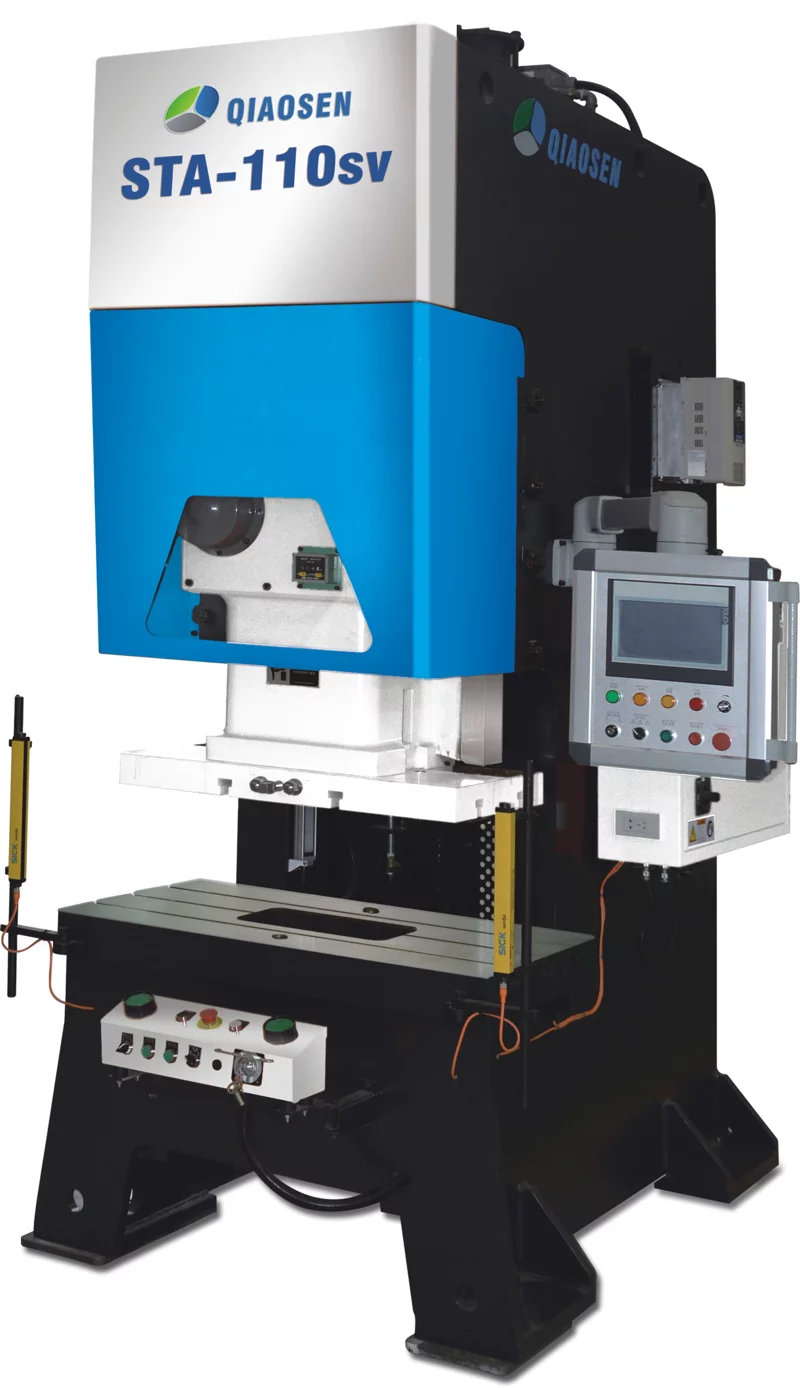
The field of industrial automation has witnessed significant advancements in recent years. One area that has seen substantial growth is the development of pneumatic presses. These machines play a vital role in various industries such as automotive, aerospace, and electronics manufacturing. Traditional pneumatic presses have been widely deployed for their cost-effectiveness and reliability. However, with the introduction of Servo Press, there has been a paradigm shift in terms of performance, accuracy, and energy efficiency. In this article, we will explore the key differences between Servo Press and conventional pneumatic presses, highlighting the benefits and limitations of each.
1. Functionality:
Conventional pneumatic presses function by converting compressed air into mechanical energy, which is then transferred to the material being worked upon. The force and speed of operation are controlled through the regulation of air pressure. On the other hand, Servo Press employ a sophisticated combination of a servo motor, ball screw, and linear guide to generate precise motion control. They provide better force and position control, enabling more accurate and repeatable operations.
2. Force Control:
One of the major differences between the two types of presses lies in their force control capabilities. Conventional pneumatic presses typically offer limited force control options. While it is possible to regulate the air pressure to adjust the applied force, it is challenging to achieve high precision force control. Servo Press, however, excel in this aspect. The servo motor employed in these machines allows for highly accurate force control, enabling operators to exert the desired force with precision.
3. Speed Control:
Traditional pneumatic presses offer relatively simple speed control mechanisms. The speed of operation is usually regulated by controlling the exhaust rate of compressed air. Although this provides basic speed adjustment, it lacks the ability to achieve optimal acceleration and deceleration profiles. In contrast, Servo Press leverage the servo motor's advanced speed control capability. This allows for precise control over the speed of operation, facilitating efficient acceleration, deceleration, and overall improved productivity.
4. Position Control:
Position control is critical in applications where parts need to be accurately aligned or inserted. Conventional pneumatic presses typically lack accurate position control capabilities. It is challenging to achieve precise positioning due to the reliance on air pressure regulation. Servo Press overcome this limitation by utilizing the servo motor's inherent position control features. These machines offer high-precision positioning, ensuring accurate placement and alignment of workpieces.
5. Energy Efficiency:
Energy efficiency is an increasingly important consideration in modern industrial practices. Conventional pneumatic presses do not excel in this aspect due to the continuous requirement of compressed air. They require a constant supply of compressed air, leading to substantial energy consumption. Servo Press, on the other hand, are designed to maximize energy efficiency. The servo motor's energy-saving features, combined with the ability to adjust force and speed accurately, result in reduced energy consumption and overall operational costs.
8years foriegn trade experience Easily grasp customer needs Keeping good relationship with customers