Solutions to Material Slippage in Punch Press Servo Feeders
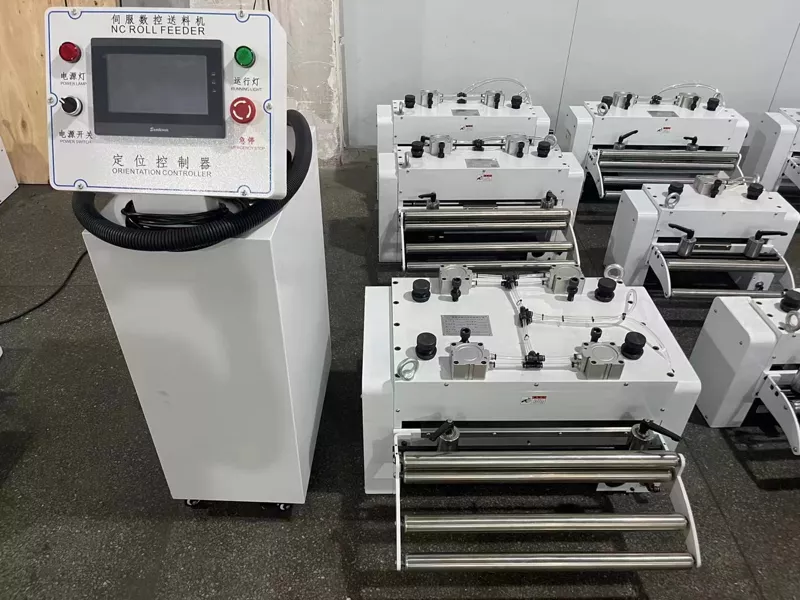
Servo feeder for punch press is a commonly used material conveying equipment in the stamping industry, which helps improve production efficiency and save labor costs for enterprises. With the widespread use of machines, we may encounter some problems in practical use to a greater or lesser extent. For example, material slipping in the servo feeder. In the eyes of industry professionals, this is a troublesome issue because material slipping can cause a series of problems, such as failure to deliver materials to the correct position, inaccurate positioning, and crushed mold parts being non-conforming. So, how should we deal with the issue of material slipping in the machine?
1. What we need to do is find out the cause of the problem and inspect the cylinder management of the pneumatic device in the servo feeder. Insufficient air pressure or insufficient air pipes can result in low air pressure and insufficient pressure springs when clamping the material. If the material is too thick, it will not be tightly clamped and is prone to sliding. In this case, another air pipe must be connected to the cylinder on the solenoid valve to provide thrust to clamp the roller on the servo feeder tighter. This will prevent slipping, and increasing the intake pressure can also increase the cylinder pressure.
2. When the servo feeder's feeding speed is met, the distance between the servo feeder and the straightening machine or material rack should be minimized to reduce the waiting zone, thereby reducing the weight of materials in the waiting zone and lightening the load to prevent excessive sliding of materials in the servo feeder under pressure.
3. Check whether the power springs of the feeding rollers are qualified and if their rebound force meets the requirements. If they do not meet the requirements, new springs need to be replaced and the pressure increased.
8years foriegn trade experience Easily grasp customer needs Keeping good relationship with customers