How to maximize the efficiency of metal stamping machine at the lowest cost
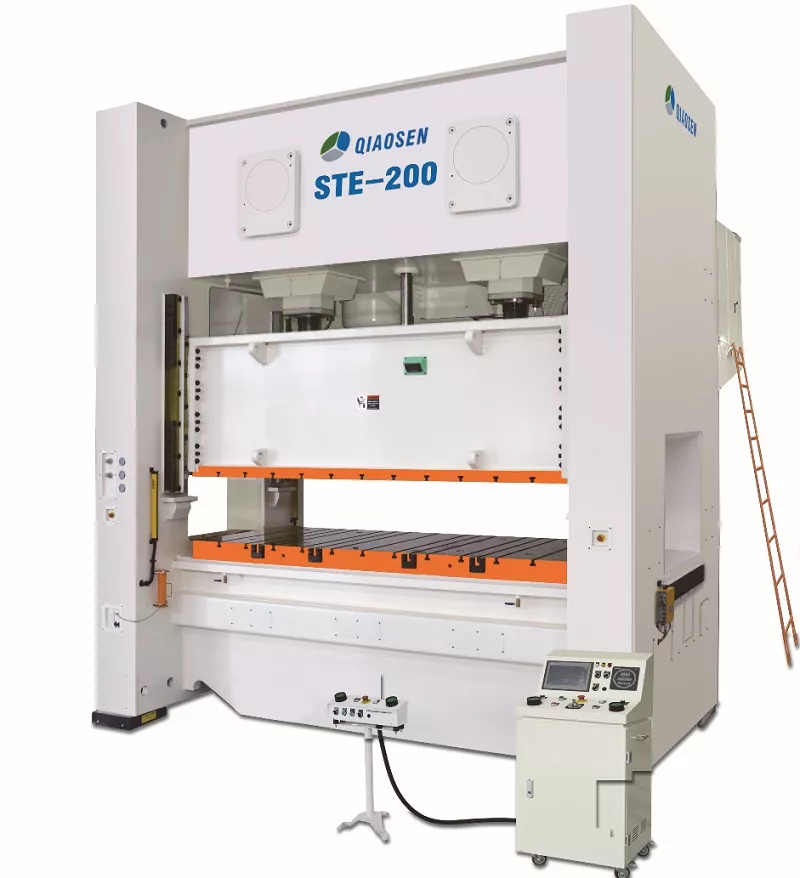
Discover effective methods to reduce the stamping cost of metal stamping machines without compromising on quality. Enhance your hardware stamping production process with industry expertise. This article presents 16 key strategies to help you make informed decisions, save costs, and maintain high standards for stamped parts.
1. Material selection:
Explore various metal options based on current market prices and stamping requirements to optimize cost savings.
2. Simplify stamping molds:
Evaluate the complexity of metal stamping machine molds and identify opportunities to simplify them, such as converting square holes to round holes to reduce production time and overall part cost.
3. Extend mold life:
Minimize downtime caused by frequent offline repairs of stamping molds. Take preventive measures to minimize tool and mold wear in your designs.
4. Streamline control plans:
Utilize existing performance data to optimize load and time costs while maintaining functionality.
5. Optimize tolerances:
Evaluate the feasibility of increasing tolerance requirements without compromising design functionality. Relaxing tolerances can significantly save costs.
6. Review specification requirements:
Stay updated on the latest standards and specifications to identify favorable changes that can lower costs and enhance productivity.
7. Optimize safety margins:
Evaluate the safety margins of metal stamping machines and make modifications when there are changes in design loads. This helps reduce costs without compromising safety.
8. Automate manual operations:
Explore opportunities to automate manual processing operations to reduce costs and production time. Utilize 3D simulation systems for automated design creation.
9. Adapt to product design changes:
Examine design changes across the entire product and adjust your stamping design while maintaining functionality. Optimize transportation by bundling parts together.
10. Utilize similarity in stamping:
Identify similar stamped parts and make adjustments to meet both requirements, thereby reducing costs.
11. Compliance with government regulations:
Stay informed about regulations regarding materials and processes to avoid cost fluctuations and production instability.
12. Optimize outsourcing services:
Consider transportation costs and integrate outsourcing services with reliable suppliers.
13. Increase automation levels:
Explore machines with higher automation capabilities to reduce production runs, tool setups, and manual processing, resulting in cost savings.
14. Efficient project management:
Collaborate with other metal stamping suppliers to provide reliable communication, quality assurance, and efficient project management, avoiding additional costs and time-consuming management.
15. Industry expertise:
Hire metal stamping partners with in-depth knowledge of your vertical market to avoid delays caused by educating them on industry-specific requirements.
16. Simplify yield:
Optimize product design as throughput increases to improve manufacturability and production time.
By implementing these strategies, you can significantly save costs, improve productivity, and maintain high-quality stamped parts.
8years foriegn trade experience Easily grasp customer needs Keeping good relationship with customers