How To Maintenance C-type Double-Crank Pneumatic Punch Press
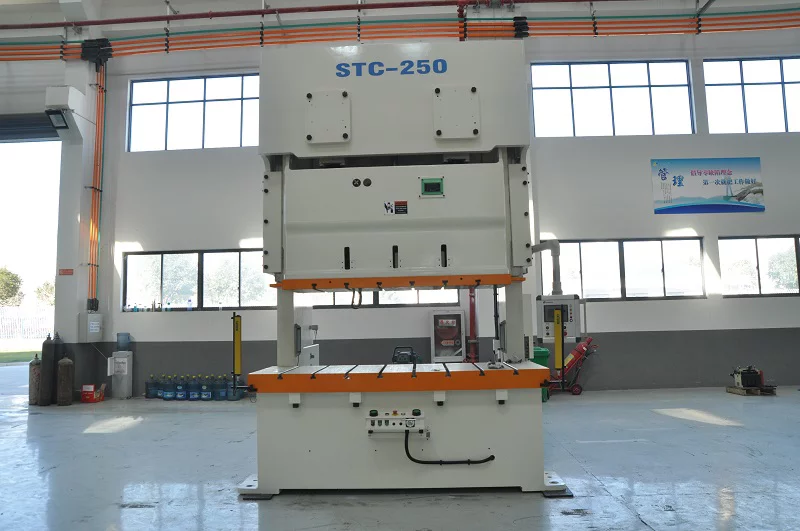
1.1 Maintenance of the Air Pressure of C-type Double-Crank Pneumatic Punch Press
a. Air Piping:
Check for any air leakage in the pipelines.
b. Air Valves and Solenoid Valves:
Verify if the control of the air valves and solenoid valves is functioning properly.
c. Balancing Cylinders:
Check for air leaks and ensure proper lubrication.
d. Cushions:
Inspect for air leaks, lubricate adequately, and tighten the fixings screws.
e. Pressure Gauge:
Examine if the needle of the pressure gauge is functioning properly.
1.2 Maintenance of the Electrical Components of C-type Double-Crank Pneumatic Punch Press
a. Electrical Controls:
Check the controllers and their response. Replace any faulty controllers and tighten any loose parts. Verify if the miniature circuit breaker is the appropriate size and inspect the insulation of the wires, replacing any damaged wires.
b. Motor:
Ensure that the motor and its brackets have tightened screws.
c. Buttons and Foot Switches:
Carefully inspect these switches and replace any faulty ones promptly.
d. Relays:
Thoroughly maintain the relays, including checking for contact point wear, loose or disconnected wires, among others.
1.3 Lubrication Maintenance of C-type Double-Crank Pneumatic Punch Press
a. Air Lubrication Components of the Clutch:
Remove any accumulated water, inspect individual components, and add lubricating oil to the correct location.
b. Lubrication System:
Follow the lubrication procedures provided in this manual to maintain the lubricated parts. Check for ruptured or worn-out lubrication lines, any leaks or damages in accessories, and ensure oil levels meet the required standards. The oil in the oil-immersed gearboxes should be replaced every three months under normal operations, and the oil tank should be cleaned every six months (approximately 1500 hours).
1.4 Mechanical Maintenance of C-type Double-Crank Pneumatic Punch Press:
a. Worktable:
Ensure no foreign objects are placed between the worktable and the frame. Confirm that the worktable locking screws are not loose, and verify the flatness of the worktable within the tolerance range.
b. Clutch:
Inspect for air leakage and check the wear condition of the friction plates.
c. Drive Gears:
Confirm tightness of gears and keys, and ensure proper lubrication of the gears.
d. Slide Adjustment Components (Motorized):
Verify the locking of the slide adjustment motor, check the automatic brake function, and lubricate the worm and worm wheel. Confirm the accuracy of the die height indicator.
e. Slide Adjustment Components (Manual):
Inspect the gear of the slide adjustment for proper lubrication. Check for any failure of the fixtures and ensure the accuracy of the die height indicator.
f. Electric Transmission:
Check for any looseness between the motor shaft and the pulleys. Inspect belts and pulleys for cracks, wear, or deformation.
g. Cleaning:
Clean the inside and outside of the punch press, removing any accumulated foreign objects.
8years foriegn trade experience Easily grasp customer needs Keeping good relationship with customers