Common Issues and Maintenance Tips for Automated Punching Machine
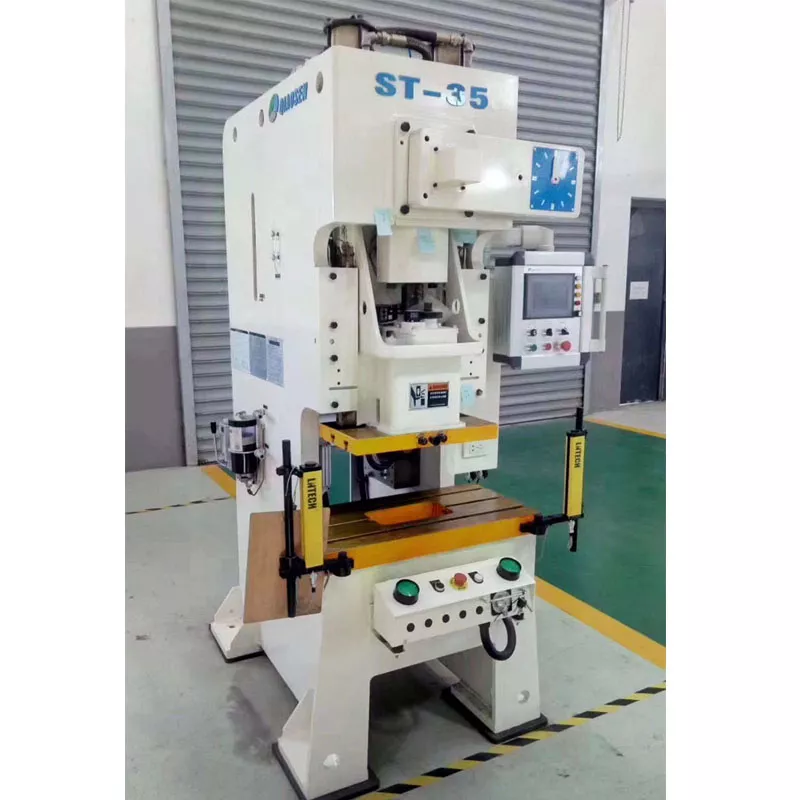
Learn how to effectively address common issues and perform regular maintenance on your automated punching machine to ensure optimal performance and prevent safety accidents. Gain insights on adjusting slider links, handling disengagement, managing comprehensive gap and slider-guide rail clearance, as well as properly maintaining brakes and clutches. Stay informed and keep your machine in top condition.
1. Locking the Slider Link on the Automated Punching Machine:
To prevent any loosening of the slider link caused by long-term use or excessive load, it is crucial to check and adjust the connecting rod lock nut promptly whenever necessary.
2. Overcoming Disengagement Phenomenon:
When the upper and lower molds are closed and the slider fails to operate correctly at the bottom dead center, reversing the motor's direction, increasing air compressor pressure, switching to the "inching" state, and incrementally pulling up the slider to the top dead center can resolve this issue.
3. Addressing Comprehensive Gap Issues:
During production, if the moving slider exhibits excessive vibration when reaching the bottom dead center, it indicates a sizable comprehensive gap that requires immediate adjustment.
4. Maintaining Optimal Slider-Guide Rail Clearance:
Avoid generating excess heat by ensuring the gap between the slider and the guide rail is adequately adjusted, neither too tight nor too loose.
5. Vital Maintenance of Brakes and Clutches:
Recognizing the critical role brakes and clutches play in automated punching machine safety, it is essential to understand their basic structure beforehand. Prior to each operation, thoroughly inspect their safety performance for any abnormal conditions such as failure to stop at the specified position, unusual sounds or vibrations, and slow slider movement. Report any anomalies promptly for timely maintenance.
8years foriegn trade experience Easily grasp customer needs Keeping good relationship with customers