Reasons for abnormal lubrication in precision punch machines
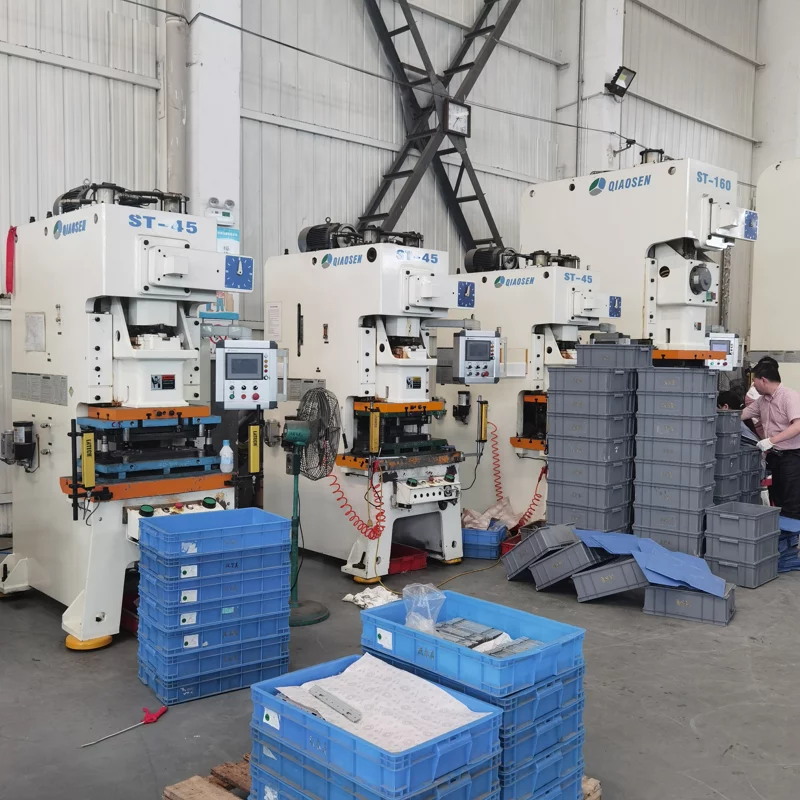
When the precision punch is in use, an electric thin oil pump is generally used to drive the lubricating oil into the oil separator, and the oil separator diverts the oil to each lubrication point according to the designed flow rate, thereby lubricating the kinematic pair. When the oil pump starts to pump oil, the valve core on the oil distributor will swing, and the micro switch on it will trigger a pulse signal to the PLC control system. If the signal is normal within the specified time, the PLC will work normally. If the signal is abnormal, it will alarm. This will cause precision What are the reasons for abnormal lubrication in punch presses?
1. During debugging, the wiring of the oil pump motor was reversed, and the oil could not be pumped in even if the motor was reversed.
2. If the lubricating oil level is too low, the oil suction port cannot absorb oil, which requires the staff to refuel to the upper limit in time.
3. There is air in the lubricating oil and the oil pressure cannot be pumped up. At this time, the air in the oil needs to be drained out, and there should be a vent button or screw plug on the oil pump.
4. The oil flowing back into the fuel tank has foreign matter blocking the filter at the oil suction port, causing the oil to fail to be sucked up. At this time, the filter needs to be checked and cleaned and new oil needs to be replaced.
5. Some lubrication points are blocked. Generally, precision punch machines use a progressive oil separator to distribute oil. If one lubrication point is blocked, the entire oil circuit will be blocked. It is necessary to check the oil circuit and each lubrication point. After the staff finds the fault point, it can be solved through cleaning methods.
8years foriegn trade experience Easily grasp customer needs Keeping good relationship with customers